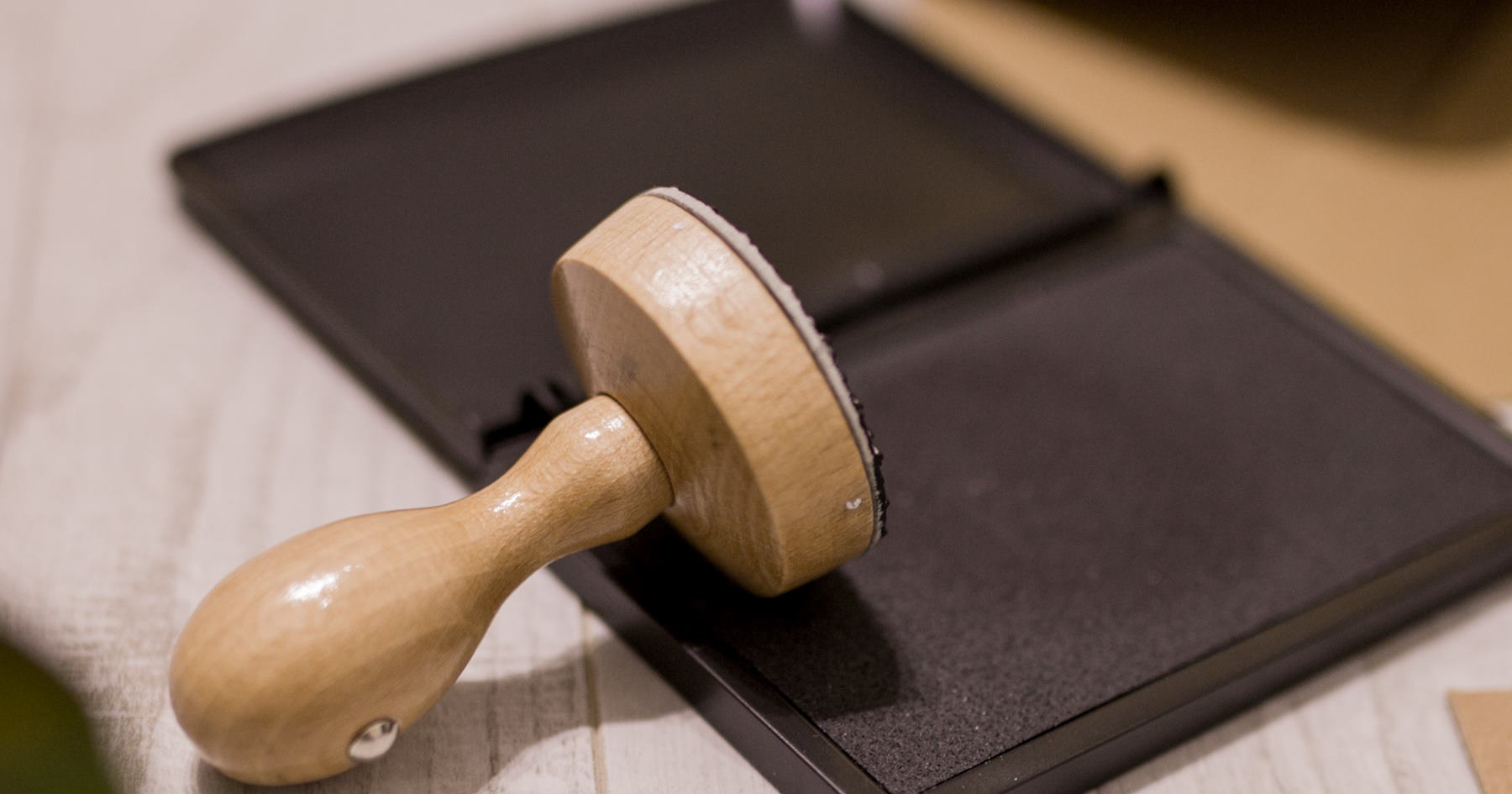
ISO 9001 is an international standard for quality management systems. It provides a framework and set of requirements that organizations can follow to ensure their products and services consistently meet customer requirements and enhance customer satisfaction. Achieving ISO 9001 certification can bring numerous benefits to an organization, including improved customer trust, enhanced efficiency, and increased competitiveness in the market.
In this article, we will delve into the key requirements for ISO 9001 certification, highlighting the steps and considerations organizations need to take to meet these requirements and obtain the certification.
Understanding ISO 9001
ISO 9001 is based on a set of quality management principles, including a strong customer focus, leadership engagement, process approach, and continuous improvement. It sets out the criteria for a quality management system and is applicable to organizations of all sizes and industries.
To meet the requirements of ISO 9001, organizations must establish and maintain a set of processes and procedures aimed at ensuring the consistent delivery of high-quality products or services. These processes should cover various aspects, including customer satisfaction, product design and development, resource management, and continual improvement.
Step 1: Getting Started
The first step in achieving ISO 9001 certification is to get familiar with the standard and its requirements. Organizations should thoroughly read the ISO 9001 standard document and understand its structure, clauses, and key concepts. It is also recommended to attend ISO 9001 training courses to gain a deeper understanding of the standard and its implementation.
During this stage, organizations should also assess their current quality management system (if any) to identify any gaps or areas that need improvement to align with ISO 9001 requirements. This gap analysis will help determine the steps needed to meet the standard.
Step 2: Leadership Commitment
ISO 9001 requires strong leadership commitment and engagement in the quality management system. Top management must demonstrate their involvement by establishing a quality policy, setting quality objectives, and ensuring resources are allocated to support the implementation and maintenance of the system.
Leadership commitment also includes promoting a quality culture within the organization, motivating employees, and regularly reviewing the effectiveness of the system.
Step 3: Documentation
ISO 9001 emphasizes the importance of documentation to define, control, and improve the organization's processes. To meet the standard's requirements, organizations must establish and maintain documented procedures and records.
The documentation should cover various aspects such as the quality policy, objectives, process descriptions, work instructions, and records of process performance. It is essential to ensure the documentation is clear, accessible, and up to date.
Step 4: Risk-based Thinking
ISO 9001:2015 introduced a new concept called risk-based thinking. Organizations must identify and address the risks and opportunities that could affect the quality management system and its ability to deliver conforming products or services.
During this step, organizations need to assess the internal and external factors that could impact their quality management system, define risk assessment procedures, and implement mitigation actions where necessary.
Step 5: Process Approach
ISO 9001 emphasizes the importance of a process approach to achieve consistent results. Organizations must identify and map their processes, determining their sequence and interaction to achieve the desired outcomes.
The process approach requires establishing clear process objectives, defining responsibilities, and monitoring the performance of the processes. By adopting a process approach, organizations can enhance efficiency, effectiveness, and overall performance.
Step 6: Implementation and Monitoring
Once the required documentation, processes, and procedures have been established, organizations need to implement the ISO 9001 system throughout the organization. This involves training employees on the requirements of the standard, ensuring their involvement and understanding of their roles in the system.
Organizations also need to establish a robust monitoring and measurement system to evaluate the performance of the quality management system. This includes conducting internal audits, collecting data, monitoring customer satisfaction, and analyzing process performance.
Step 7: Continual Improvement
ISO 9001 promotes a culture of continual improvement. Organizations must actively seek opportunities for improvement, both in terms of their processes and the overall effectiveness of the quality management system.
This step involves analyzing data, identifying areas for improvement, implementing corrective actions, and monitoring the effectiveness of these actions. By continually improving the system, organizations can enhance customer satisfaction, reduce inefficiencies, and achieve better business results.
Conclusion
ISO 9001 certification is a valuable recognition of an organization's commitment to quality and customer satisfaction. By following the requirements outlined in the standard, organizations can establish effective quality management systems that drive continuous improvement and enhance their competitiveness in the market.
Achieving ISO 9001 certification requires careful planning, strong leadership commitment, and a systematic approach to quality management. By understanding and implementing the key requirements of ISO 9001, organizations can reap the benefits of improved processes, enhanced customer trust, and sustainable growth.